Co trzeba wiedzieć, żeby zacząć automatyzować magazyn?
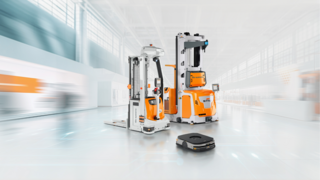
Punktem wyjścia do podjęcia trafnych decyzji na temat opłacalności i wykonalności wdrożenia automatyzacyjnego jest zawsze gromadzenie danych. O co w pierwszej kolejności pytają eksperci?
Według prognoz Next Move Strategy Consulting wartość globalnego rynku robotyki wzrośnie w 2024 roku o 16% i osiągnie wartość 8,36 mld dolarów. Analitycy przewidują, że będzie się to wiązać ze wzrostem popularności AGV, AMR, AS/RS, robotów współpracujących, dronów magazynowych, systemów G2P czy
przegubowych robotycznych ramion. Niezależnie od typu wdrażanych rozwiązań, pierwszym krokiem do realizacji jest analiza procesu magazynowego i identyfikacja potencjału automatyzacji transportu wewnętrznego. Jakie kwestie są na tym etapie kluczowe opowiedział nam Dominik Jasiok, Advanced Applications Manager STILL Polska.
Dane potrzebne do zaplanowania automatyzacji
Pierwszym krokiem do weryfikacji potencjału automatyzacji i przystąpienia do opracowania jej koncepcji jest zebranie danych na temat specyfiki ładunków, tras przejazdu oraz możliwych sposobów generowania zleceń.
Specyfika ładunków
W pierwszej kolejności zbieramy dane na temat specyfiki obsługiwanych w zakładzie ładunków. Kluczową kwestią jest to, czy w obiekcie korzysta się ze standardowych europalet. Kontrolowane muszą być nie tylko ich szerokość i długość, ale także wysokość. Wynika to z konieczności skonfigurowania punktów odniesienia dla czujników umieszczonych na widłach AGV , za których pomocą wózki automatyczne orientują się względem palety podczas jej pobierania. Nietypowe nośniki ładunku mogą zwiększać koszty lub wręcz uniemożliwić automatyzację. Ze względów bezpieczeństwa znaczenie ma także analiza występowania sytuacji, w których ładunki wystają poza obrys palety.
Trasy przejazdów
Kiedy już wiemy, jak wygląda to, co mamy wozić, trzeba dowiedzieć się, skąd dokąd ma być to wożone. W tym celu potrzebujemy komputerowego pliku z układem magazynu w formacie przyjaznym programom typu AutoCAD. Na tej podstawie weryfikujemy, czy korytarze są dość szerokie. Jesteśmy też w stanie obliczyć długość tras i skalkulować optymalne ścieżki przejazdu. Jest to punktem wyjścia do określenia:
- liczby wózków automatycznych potrzebnych do realizacji zadań,
- koniecznej częstotliwości przejazdów.
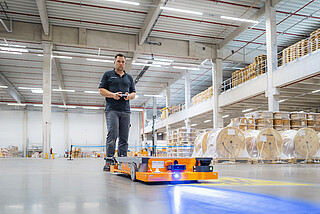
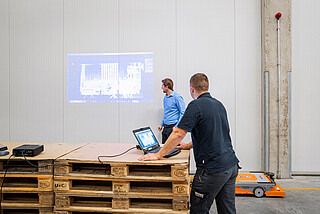
Sposób wywołania zlecenia
Mamy dane – i co dalej?
Na podstawie informacji na temat ładunków, tras przejazdu i sposobu generowania zleceń da się zweryfikować wykonalność oraz przygotować pierwszy budżet projektu. Kalkulujemy liczbę wózków pozwalających bezpiecznie wykonać zakładane zadania oraz nakład
pracy konieczny do integracji wszystkich systemów. Jeśli wdrożenie jest technicznie możliwe, a koszty inwestycji i czas zwrotu z niej akceptowalne dla klienta, przystępujemy do doskonalenia i uszczegółowiania koncepcji automatyzacji.