Kiedy pracownicy śpią, AGV działają
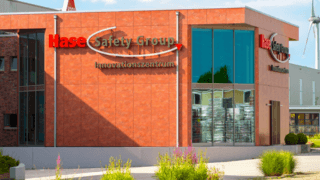
Dzięki wdrożeniu automatycznego składowania w oparciu o wózki AGV w technologii STILL iGo systems firma Hase Safety Group zwiększyła przepustowość magazynu bez zwiększania zatrudnienia ani wprowadzania zmianowego trybu pracy.
Na skróty:
Z myślą o rozwoju i zaspokojeniu rosnącego popytu na środki ochrony osobistej, Hase Safety Group zbudowało obiekt logistyczny o powierzchni 4 tys. mkw. mogący pomieścić 10 tys. miejsc paletowych.
- Znając uwarunkowania rynku pracy inwestor dążył do tego, by rozbudowa pozwoliła zwiększyć przepustowość magazynów firmy bez konieczności zwiększania zatrudnienia.
- Po przeanalizowaniu specyficznych dla zakładu uwarunkowań procesów logistycznych dostawca zaproponował stworzenie magazynu z bardzo wąskimi alejkami i wysokimi regałami
- Obsługę zadań składowania i pobierania ładunków powierzono wózkom automatycznym, a prace zorganizowano tak, żeby wybrane procesy mogły toczyć się bez udziału ludzi.
- Autonomiczne, współpracujące ze sobą i samodzielnie ładujące baterie wózki widłowe AGV przewożą ładunki przez całą dobę. Dzięki temu udało się znacząco zwiększyć przepustowość magazynów bez konieczności zwiększania zatrudnienia i wprowadzania zmianowego trybu pracy.
Charakter przedsiębiorstwa, w którym dokonano wdrożenia
Nazwa: Hase Safety Group
Obszar działalności: produkcja środków ochrony osobistej
Miejsce wdrożenia: Jever, Dolna Saksonia, Niemcy
Historia Hase Safety Group AG sięga 1937 r. Choć w tym czasie firma przeniosła się z Gdańska do Niemiec i z rodzinnego interesu przeistoczyła się w grupę kapitałową z kilkoma niezależnymi spółkami, do dziś głównym obszarem jej działalności jest wytwarzanie środków ochrony osobistej. Na przestrzeni lat asortyment się poszerzył. Dziś – obok rękawic roboczych – przedsiębiorstwa tworzące Hase Safety Group wytwarzają także odzież i obuwie robocze oraz wyposażenie ochronne. Zachowując dążenie do rozwoju i ekspansji, w 2020 roku firma zdecydowała się na rozbudowę swojej siedziby w miejscowości Jever. Powstało wówczas centrum innowacji i szkoleń, showroom oraz nowy dział rozwoju produktów. Powierzchnię magazynową rozbudowano wówczas o nowoczesny obiekt o powierzchni 4 tys. mkw. z 10 tys. miejsc paletowych i szeregiem rozwiązań automatyzacyjnych, dzięki którym Hase Safety Group jest gotowa na logistyczne wyzwania przyszłości.
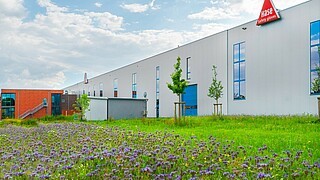
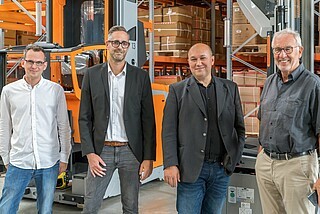
Automatyzacja w oparciu o przenośniki, wózki systemowe i podnośnikowe
Hase Safety Group
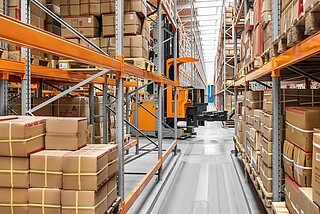
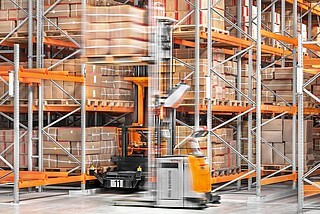
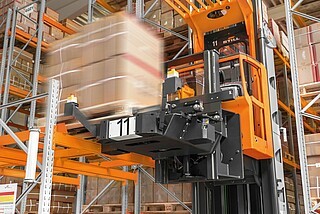
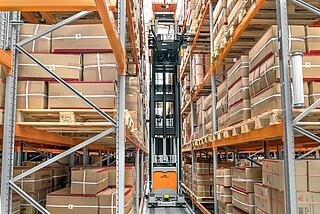
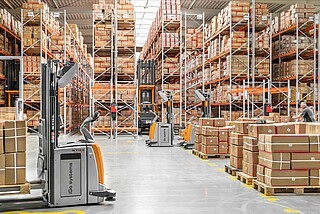
Cel wdrożenia:
- Rozbudowa powierzchni magazynowej
- Zwiększenie przepustowości magazynu bez zwiększania zatrudnienia
Wdrożone rozwiązanie intralogistyczne:
- Analiza i optymalizacja procesów, dostaw i tras przejazdu w ramach doradztwa intralogistycznego STILL
- Automatyzacja procesów w oparciu o technologię STILL iGo systems wózki systemowe VNA STILL MX-X oraz wózki podnośnikowe STILL EXV-SF
- System ładowania pozwalający wózkom na uzupełnianie pojemności baterii bez udziału operatora
Pierwszym krokiem do zaprojektowania rozwiązania była wnikliwa analiza całego procesu przyjmowania, składowania i wydania towarów, dająca podstawy do zaproponowanie usprawnień możliwych do uzyskania dzięki nowemu obiektowi magazynowemu.
Ostatecznie ładunki przychodzące są wstępnie transportowane przy użyciu teleskopowego przenośnika taśmowego. Następnie pracownicy rozdzielają i paletyzują pudła przy pomocy próżniowych urządzeń podnoszących. Posortowane ładunki są wysyłane na stanowiska materiałów przychodzących, gdzie po wskanowaniu do systemu są przejmowane przez AGV odpowiedzialne za zadania związane ze składowaniem. Automatyczne wózki podnośnikowe STILL EXV iGo systems pobierają palety i transportują je następnie do automatycznego stanowiska kontroli konturu. Jeśli ładunek przejdzie ją pozytywnie, jest przewożony do punktu transferowego przy magazynie gęstego składowania z bardzo wąskimi korytarzami. Stamtąd pracę przejmują automatyczne wózki systemowe STILL MX-X iGo systems. Gdy towary są pobierane, proces przebiega w odwrotnej kolejności: MX-X transportuje paletę do strefy przeładunku, z której pobiera ją wózek EXV i przewozi albo do magazynu ręcznej kompletacji, albo bezpośrednio do punktu załadunku samochodów ciężarowych. Po zakończeniu realizacji zadań wózki AGV automatycznie wracają do swoich pozycji w oczekiwaniu na następne zadanie.
Dodatkowe korzyści uzyskano dzięki zastosowaniu do zasilania wózków nowoczesnego systemu fotowoltaicznego o powierzchni ponad 10 000 mkw. Dostarcza on zielonej energii do ładowania akumulatorów pojazdów transportu wewnętrznego. W razie potrzeby AGV samoczynnie przemieszczają się do stacji ładowania. Dzięki ładowarkom podłogowym nie ma potrzeby podłączania żadnych przewodów. Automatyczne wózki widłowe są więc w stanie ładować swoje akumulatory przez noc – bez angażowania personelu.
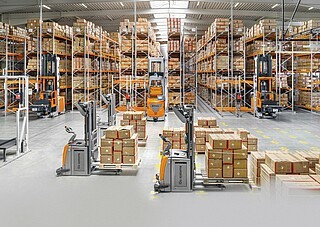
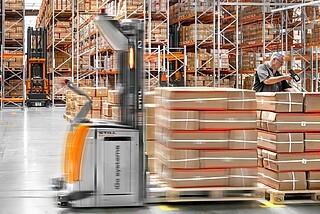
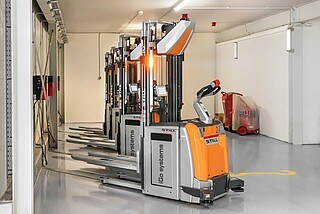

Doradztwo logistyczne pozwoliło przygotować się na przyszłość
- Uzyskanie wysokiej gęstości składowania i optymalnego zagospodarowania przestrzeni magazynowej
- Poprawa bezpieczeństwa pracy w efekcie optymalizacji tras przejazdu i zmniejszenia natężenia ruchu
- Zwiększenie przepustowości procesów intralogistycznych bez zwiększania zatrudnienia
Najważniejszą korzyścią wynikającą z wzniesienia zautomatyzowanego obiektu jest znaczący wzrost przepustowości magazynu bez zwiększenia zatrudnienia. Dzięki automatyzacji procesy magazynowe mogą być realizowane wieczorami i nocami bez obecności personelu. Pomimo rosnącego popytu na odzież ochronną, nowy system pozwala w efekcie terminowo realizować otrzymywane zamówienia bez konieczności wprowadzania pracy w trybie wielozmianowym. Ważną cechą wdrożonego sposobu organizacji procesów magazynowych jest także wysoka gęstość składowania. Zastosowanie wielokondygnacyjnych regałów podzielonych bardzo wąskimi alejkami wraz z komplementarnymi automatycznymi wózkami systemowym zapewnia optymalne zagospodarowanie przestrzeni magazynowej. Optymalizacja tras przejazdu zmniejsza natomiast natężenie ruchu, niwelując zapotrzebowanie na energię oraz przyczyniając się do poprawy bezpieczeństwa pracy podczas zmian, na których obecni są ludzie.
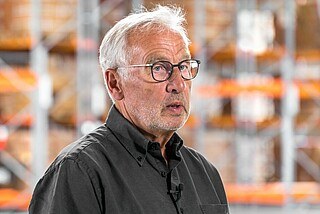
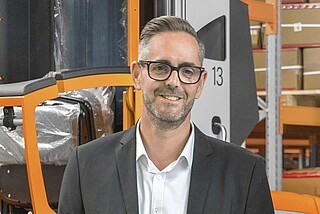
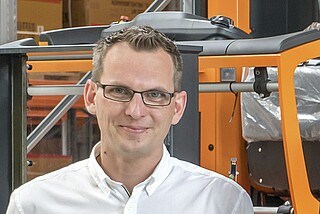