Jak automatyzacja poprawiła KPI magazynu Fabory
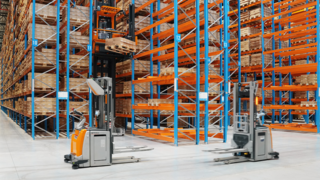
Nowy magazyn automatyczny pozwolił firmie Fabory skrócić czas dostaw produktów do klientów i obniżyć koszty operacyjne. Co więcej, do dziennej obsługi kilkuset palet wystarczy zaledwie po dwóch pracowników magazynowych na jedną zmianę.
Na skróty:
- Firma Fabory poszukiwała sposobu na zwiększenie przepustowości magazynu bez potrzeby rekrutacji dużej liczby nowych pracowników.
- Naturalnym kierunkiem poszukiwań były automatyzacyjne rozwiązania transportu wewnętrznego i składowania.
- Jako partnera technologicznego i dostawcę wybrano firmę STILL.
- By zaspokoić potrzeby Fabory, stworzono magazyn wysokiego składowania na 28 tys. miejsc paletowych obsługiwany przez automatyczne wózki podnośnikowe i systemowe EXV iGo oraz MX-X iGo.
- Do obsługi obiektu będącego w stanie przyjmować 150-300 palet dziennie wystarczą dwie osoby. Udało się obniżyć koszty operacyjne i zwiększyć bezpieczeństwo pracy.
Charakter przedsiębiorstwa, w którym dokonano wdrożenia
Nazwa: Fabory
Obszar działalności: Branża przemysłowych elementów złącznych oraz precyzyjnych komponentów mechanicznych
Miejsce wdrożenia: Główny obiekt magazynowy Fabory, Tilburg, Holandia
Marka Fabory powstała w 1947 r. Na przestrzeni lat stojąca za nią firma stała się międzynarodowym potentatem branży przemysłowych elementów złącznych i precyzyjnych komponentów mechanicznych. Jej liczący ponad 450 tys. pozycji asortyment dostarczany jest z 5 centrów dystrybucji do kilkunastu europejskich krajów. Mieszczący się przy siedzibie głównej w Tilburgu obiekt logistyczny został rozbudowany z użyciem rozwiązań automatyzacyjnych pozwalających osiągnąć dużą gęstość składowania. Wdrożone systemy regałow liczą 12 metrów wysokości i pozwalają na dostęp do każdego ze znajdujących się w tej strefie 28 tys. miejsc paletowych. Jako dostawcę infrastruktury i wózków widłowych – zarówno automatycznych, jak i sterowanych ręcznie – wybrano firmę STILL.
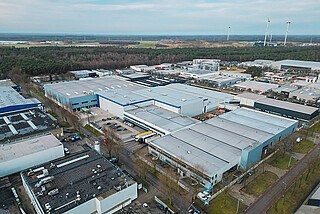
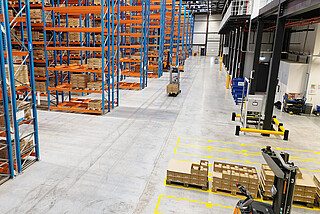
Rozwiązanie: magazyn automatyczny z wózkami podnośnikowymi i systemowymi
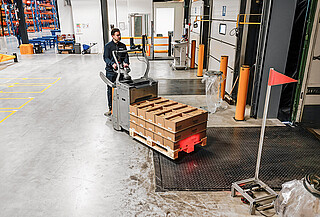
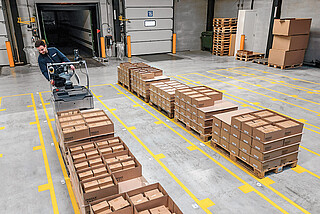
Cel wdrożenia:
- Zwiększenie przepustowości magazynu dzięki rozwiązaniom automatyzacyjnym
Zastosowane rozwiązanie intralogistyczne:
- Opracowanie kompleksowej koncepcji transportu wewnętrznego
- Integracja WMS i systemu zarządzania wózkami z SAP
- Zaprojektowanie obsługiwanej ręcznie z pomocą wózków unoszących EXH-SF strefy odbioru ładunków
- Flota samodzielnych i współpracujących ze sobą wózków automatycznych AGV – podnośnikowych EXV iGo i systemowych MX-X iGo
Droga ładunków zaczyna się w strefie odbioru z dokami dla samochodów ciężarowych. Palety są pobierane z użyciem sterowanych ręcznie wózków unoszących z platformą dla operatora serii STILL EXH-SF . Podczas wjazdu do magazynu stacjonarny skaner automatycznie odczytuje etykietę ładunku. Po jego odłożeniu w wyznaczonym miejscu w strefie odbioru, zadania związane z transportem wewnętrznym i składowaniem przejmuje zautomatyzowany system STILL.
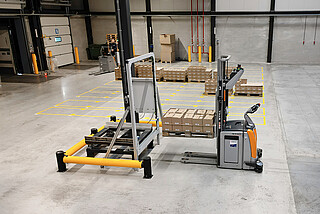
W pierwszej kolejności automatyczne wózki podnośnikowe transportują palety do pobliskiego punktu kontroli masy i obrysu ładunku. Na podstawie informacji z etykiety oraz zgromadzonych tu danych system przypisuje pozytywnie zweryfikowanym towarom optymalne miejsce składowania. Pojazdy klasy AGV serii STILL EXV iGo przenoszą ładunki do stacji transferowych na końcu regałów. Stąd są one pobierane i umieszczane na przypisanych miejscach paletowych przez automatyczne wózki systemowe VNA MX-X iGo. Trasy automatycznych wózków podnośnikowych i systemowych ustalono tak, by nigdy się nie przecinały.
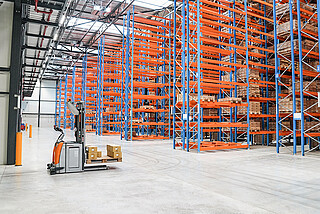
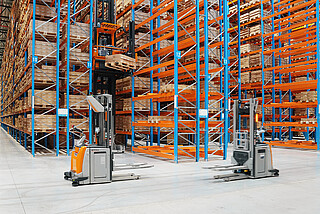
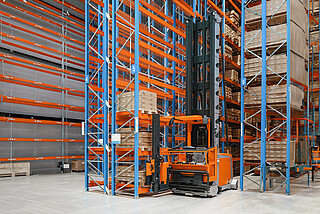
W przypadku potrzeby rozparcelowania palety jest ona najpierw transportowana do stacji transferowej przez MX-X iGo. Następnie podejmuje ją wózek podnośnikowy AGV i przewozi do punktu przeładunkowego z robotycznym ramieniem, które depaletyzuje ładunki i umieszcza je na przenośniku. Z jego pomocą opakowania trafiają pojedynczo do zautomatyzowanego magazynu małych części lub innego stosownego miejsca. System pozwala wydajnie obsługiwać 150-300 palet dziennie. Ładowanie baterii wózków automatycznych realizowane jest samoczynnie w okresach nieaktywności lub gdy akumulator osiągnie ustaloną wartość krytyczną.
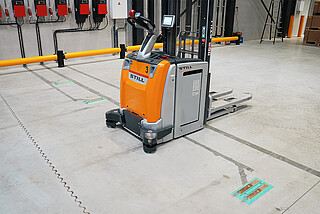
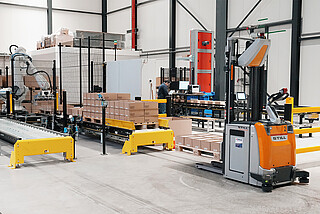
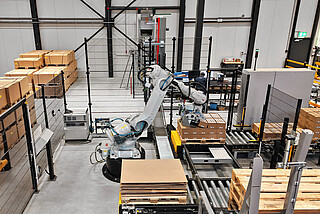
Efekt: Wydajny magazyn automatyczny wysokiego składowania
Rezultat wdrożenia:
- Magazyn zdolny funkcjonować przy zaledwie dwuosobowej obsadzie
- Wysokie bezpieczeństwo pracy
- Niskie koszty operacyjne
- Skrócenie czasu dostaw do klientów
– Bardzo podobała nam się współpraca ze STILL. Otrzymaliśmy wsparcie koncepcyjne i mogliśmy doświadczyć otwartej komunikacji. Nade wszystko jednak dotrzymaliśmy harmonogramu i zmieściliśmy się w budżecie – mówi Leon Broere, Project Manager w Fabory. – Rozwiązanie umożliwia funkcjonowanie magazynu wbrew trudnej sytuacji na rynku pracy. Do skutecznej obsługi ładunków wystarczy dwóch pracowników na zmianę. Pracujemy w trybie 2-zmianowym przez 5 dni w tygodniu. Wszyscy są bardzo zadowoleni – dodaje.
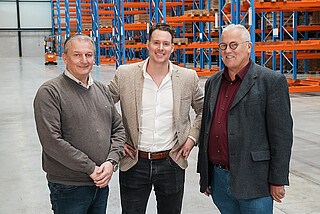
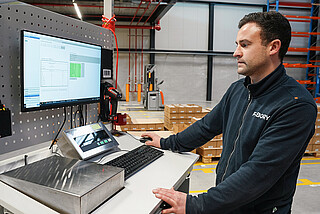
– Nowy magazyn pozwolił wprowadzić innowacje w zarządzaniu zapasami i obniżyć koszty operacyjne. Zwiększyliśmy bezpieczeństwo i elastyczność na szczyty logistyczne – relacjonuje Joost Jansonius, Logistics Director Fabory. – Czas dostawy skrócił się z jednego – dwóch dni do dwóch – trzech godzin. Nasi klienci zauważają tę różnicę – podsumowuje.