LAPP stawia na bezpieczeństwo
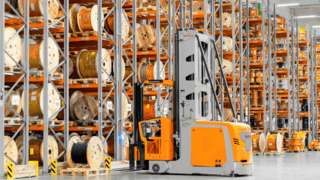
Odpowiedzią LAPP na zwiększony popyt i poszerzenie asortymentu produktów była modernizacja centrum logistycznego w oparciu o rozwiązania bezpieczeństwa pozwalające pracować z maksymalną wydajnością i przy niskich kosztach eksploatacji.
Na skróty:
-
Firma LAPP GmbH zdecydowała o modernizacji centrum dystrybucji w Hannowerze.
-
Za punkt wyjścia do zwiększenia wydajności i efektywności kosztowej funkcjonowania floty wzięto bezpieczeństwo i ergonomię.
-
W toku współpracy z doradcami intralogistycznymi STILL wdrożono system transportu wewnętrznego zintegrowany z innowacyjnymi rozwiązaniami bezpieczeństwa.
-
Bezpieczeństwo pracy przekłada się na jej wysokie tempo i niskie koszty.
Charakter przedsiębiorstwa, w którym dokonano wdrożenia
Nazwa: U.I. Lapp GmbH
Obszar działalności: Produkcja przewodów
Miejsce wdrożenia: Centrum dystrybucji, Hanower, Niemcy
LAPP powstało w 1959 r. jako rodzinna firma, gdy Oskar Lapp zaprojektował swój pierwszy przewód sterowniczy ÖLFLEX®. Choć obecnie – ponad 60 lat później – przedsiębiorstwem wciąż zarządzają potomkowie założyciela, LAPP to dziś działająca globalnie grupa z rocznymi obrotami przekraczającymi 1 mld euro. Nowoczesna sieć jej europejskiej dystrybucji opiera się na centrach logistycznych w Ludwigsburgu, Hanowerze, Stuttgarcie i Wrocławiu. Aby zagwarantować szybkie czasy dostaw w przyszłości - z uwzględnieniem potrzeb wynikających z rozwoju asortymentu – zdecydowano o przeorganizowaniu procesów transportowych oraz modernizacji obiektu logistycznego w Hanowerze. W projektowanie centrum dystrybucyjnego zaangażowani zostali doradcy intralogistyczni STILL. Zastosowano w nim szereg innowacyjnych rozwiązań, w tym radiowe systemy bezpieczeństwa i system kompensacji nierówności podłoża.
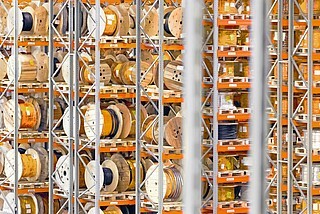
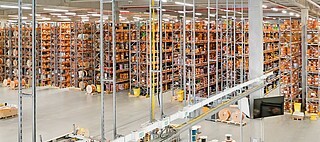
Rozwiązanie: całościowy system bezpieczeństwa magazynu - od wózków po dodatkowe usługi
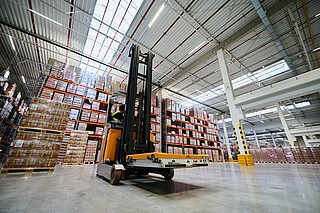
Cel wdrożenia:
- skuteczna obsługa zróżnicowanego asortymentu,
- stworzenie niepodatnego na zakłócenia wynikające z nierówności posadzki systemu transportu wewnętrznego,
- integracja wdrożonych rozwiązań z całościową koncepcją bezpieczeństwa.
Wdrożone rozwiązanie intralogistyczne:
- całościowy projekt przygotowany w oparciu o doradztwo intralogistyczne STILL i wykorzystujący m.in.:
- zaawansowane systemy bezpieczeństwa,
- systemy regałowe STILL,
- wózki systemowe VNA STILL MX-X,
- system kompensacji nierówności podłoża STILL AFC,
- czołowe elektryczne wózki widłowe z przeciwwagą serii STILL RX 20 i RX 60,
- serwis wózków widłowych STILL.
Cyfrowy system bezpieczeństwa pracy wózków widłowych w LAPP
Wraz z presją na tempo realizacji zadań rośnie ryzyko błędów i wypadków. Punktem wyjścia do projektowania nowego, charakteryzującego się w założeniu ponadprzeciętną wydajnością pracy centrum dystrybucji było bezpieczeństwo pracowników. Celem minimalizacji prawdopodobieństwa niepożądanych zdarzeń w pierwszej kolejności zidentyfikowano i oceniono potencjalne zagrożenia. Rejestrowano w tym celu przebieg procesów i trasy przejazdu wózków widłowych w centrum logistycznym LAPP. Po analizie zdecydowano o wyposażeniu pojazdów w radiowy system wspomagający ochronę przed kolizją. Składają się na niego:
- aktywne zestawy anten 360 stopni,
- elementy pasywne przy drzwiach i ruchliwych skrzyżowaniach,
- interfejs operatora komunikujący się z systemem sterowania wózka widłowego.
W razie niebezpieczeństwa system wspomagania jazdy zmniejsza prędkość pojazdu i emituje sygnały dźwiękowe i wizualne. Gdy wózek widłowy wjedzie w potencjalnie niebezpieczną strefę, natychmiast otrzyma wszystkie informacje potrzebne do aktywacji predefiniowanych funkcji bezpieczeństwa. System jest w stanie nie tylko ingerować w pracę wózka, ale także wchodzić w interakcje z otoczeniem, np. automatycznie otwierać drzwi do hali czy włączać oświetlenie w pomieszczeniu.
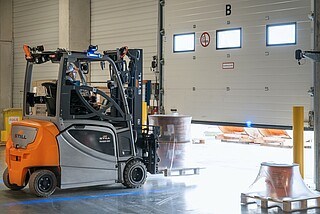
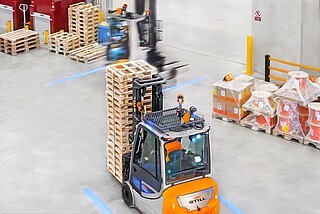
Wózki systemowe VNA z systemem kompensacji nierówności podłoża
W przypadku przeznaczonych do pracy na dużych wysokościach wózków systemowych VNA serii STILL MX-X wdrożono także system kompensacji nierówności podłoża STILL AFC. Rozpoznaje on nierówności posadzki dzięki czujnikom na kołach nośnych i w czasie rzeczywistym dynamicznie poziomuje ramę wózka, utrzymując maszt w idealnym pionie. System zapobiega drganiom, zanim one wystąpią – także przy jeździe z maksymalną bezpieczną prędkością.
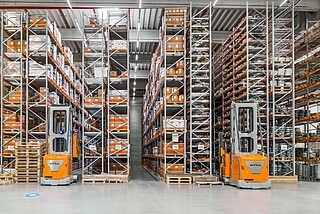
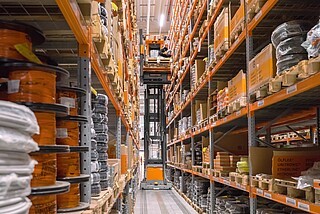
Serwis wózków widłowych kluczem do braku przestojów oraz wydajnej i bezpiecznej eksploatacji floty
Pozytywny wpływ na bezpieczeństwo ma także kompleksowa współpraca serwisowa z dostawcą floty transportu wewnętrznego. Na usługę składają się:
- scyfryzowane plany napraw i serwisowania prewencyjnego,
- szybkie interwencje techników serwisu w razie awarii i przywracanie przepływu materiałów,
- niezwłoczny dostęp do oryginalnych części zamiennych.
Podczas wizyt technicy serwisu wózków widłowych dzielą się z klientem know-how i podpowiadają, jak dodatkowo poprawić bezpieczeństwo i na jakie aspekty funkcjonowania wózków widłowych zwracać uwagę, by unikać przestojów.
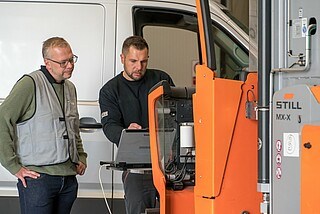
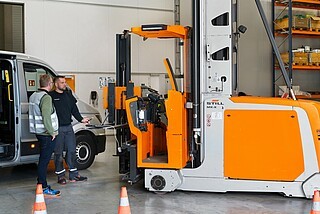
Efekt: bezpieczeństwo skutkujące wydajnością pracy i niskimi kosztami eksploatacji floty
Rezultaty wdrożenia:
- wysoki poziom bezpieczeństwa przy dużej wydajności pracy,
- ograniczenie kosztów eksploatacji floty,
- krótkie czasy dostaw do klientów.
W konkurencyjnym środowisku kluczem do sukcesu jest płynny i szybki transport wewnętrzny. Inteligentne rozwiązania STILL wspomagające operatora zwiększają bezpieczeństwo pracy przy jej wysokiej wydajności. Nowoczesne systemy wsparcia pomagają unikać wypadków, a w efekcie – uszczerbku na zdrowiu pracowników oraz uszkodzeń infrastruktury i produktów. Bezpieczeństwo przekłada się na wydajność i produktywność i pozwala redukować koszty eksploatacji floty. Dzięki wydajnemu funkcjonowaniu bez przestojów LAPP zapewnia klientom krótkie terminy dostaw.