SCHOTT: RX 60-80 i największy z teleskopów
Na skróty:
ELT (ang. Extremely Large Telescope – ekstremalnie duży teleskop) ma od 2025 r. pozwolić obserwować wszechświat 16-krotnie bardziej dokładnie niż teleskop Hubble’a
- Europejskie Obserwatorium Południowe zleciło odlanie lustra wtórnego specjalistycznej niemieckiej hucie szkła i ceramiki SCHOTT AG
- Ze względu na restrykcyjne wymagania co do precyzji procesu odlewniczego do transportu kadzi wykorzystano elektryczne wózki widłowe STILL RX 60-80
Charakter przedsiębiorstwa, w którym dokonano wdrożenia
Nazwa: SCHOTT AG
Obszar działalności: Produkcja ceramiki i specjalistycznego szkła
Miejsce wdrożenia: Zakład produkcyjny w Moguncji
Grupa SCHOTT AG to globalne, innowacyjne przedsiębiorstwo działające w branży szkła i ceramiki szklanej. Od zastosowań domowych, przez farmację, elektronikę i optykę aż po szyby samolotów – zatrudniające w sumie ponad 15 tys. osób zakłady i biura firmy w 34 krajach handlują szkłem rozmaitych rodzajów i w najróżniejszych postaciach, wypracowując roczny obrót na poziomie 2,08 mld euro. Jednym z bardziej spektakularnych – i zarazem wymagających – projektów SCHOTT w ostatnim czasie było wyprodukowanie elementów składających się na lustro największego w historii ludzkości teleskopu optycznego – mającego trafić na chilijską Pustynię Atacama ELT (angielski skrót od Extremely Large Telescope – „ekstremalnie duży teleskop”).
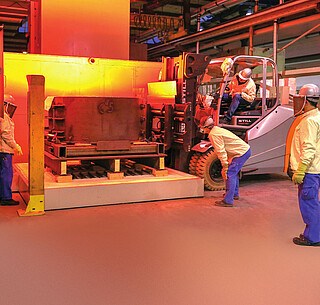
Cel wdrożenia oraz zastosowane rozwiązania intralogistyczne
Cel wdrożenia:
- Precyzyjny i bezpieczny transport kadzi odlewniczych wykorzystanych w produkcji Zeroduru® na zwierciadło wtórne ELT
Wdrożone rozwiązanie:
czołowy wózek elektryczny STILL RX 60-80
By ELT mógł działać zgodnie z ambitnymi planami, każdy z 798 sześciokątnych segmentów 39-metrowego lustra musi być dopasowany do pozostałych z dokładnością do 2 nanometrów. Dlatego też kluczowe jest, by materiał, z którego zostaną wykonane charakteryzował się minimalnym współczynnikiem ekspansji termicznej. Dlatego też firma SCHOTT AG zdecydowała się użyć bardzo odpornego na wahania temperatur produktu o nazwie Zerodur®. Ze względu na wzrost popytu na tego typu rozwiązania – także na potrzeby ELT - przedsiębiorstwo zainwestowało w nowe odlewnie i kadzie oraz pozwalający obsłużyć je sprzęt intralogistyczny. Zdecydowano się na elektryczny wózek czołowy STILL RX 60 o udźwigu na poziomie 8 ton. Dla decyzji o wyborze tego modelu wózka kluczowe były takie jego parametry jak: precyzja i płynność przemieszczeń hydraulicznych, kompaktowość, zwrotność i stabilność zapewniające, że nic nie zakłóci delikatnego procesu powstawania tafli Zeroduru®. Zastosowane w RX 60-80 zaawansowane technologicznie zawory proporcjonalne sprawiają, że ruchy wideł w pionie można kontrolować w każdym calu. Doskonałą precyzję i bezpieczeństwo jazdy zapewniają także: całkowita szerokość robocza na poziomie 4999 mm, promień skrętu wynoszący 3007 mm oraz wahliwa oś skrętna dająca zwrotność i stabilność. Punkt ciężkości jest umieszczony nisko, by żaden manewr nie był w stanie zachwiać wózkiem. Nie bez znaczenia w otoczeniu wymagającym dużej ostrożności jest również komplet rozwiązań gwarantujących doskonałą widoczność: nisko osadzone siłowniki, panoramiczne okna, kabina przesunięta nieco w bok i podwyższone siedzenie operatora – wszystko to, by ładunek ani nic innego nie blokowało linii wzroku na trasę wózka.
Efekty wdrożenia i wynikające z niego korzyści
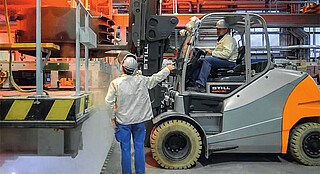
bezpieczeństwo i precyzja transportu kadzi na nowych stanowiskach odlewniczych
- minimalizacja śladu węglowego procesów intralogistycznych realizowanych w zakładzie SCHOTT AG w Moguncji
Ergonomia i bezpieczeństwo oferowane przez STILL RX 60-80 przekonały firmę SCHOTT do wyposażenia nowego, strategicznie istotnego dla rozwoju zakładu stanowiska odlewniczego w wózek tego typu. Najwyższa efektywność energetyczna w tej klasie pojazdów pozwala dodatkowo minimalizować ślad węglowy procesów i wzorowo spełniać sformułowane przez SCHOTT wymogi polityki zrównoważonego rozwoju.