Westerwald przechodzi na wózki elektryczne
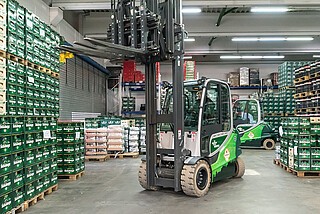
Na skróty:
Zgodnie ze swoim motto „Zachowywać to, co dobre i być otwartym na nowe” browar Westerwald-Brauerei poszukuje innowacyjnych metod warzenia tradycyjnego piwa
- Jednym z elementów modernizacji przedsiębiorstwa w ostatnich latach było zastąpienie spalinowych wózków widłowych elektrycznymi
- Obecnie 100% energii wykorzystywanej przez browar pochodzi ze źródeł odnawialnych, a flota intralogistyczna generuje niższe koszty eksploatacji i gwarantuje operatorom wyższy komfort pracy
Charakter przedsiębiorstwa, w którym dokonano wdrożenia
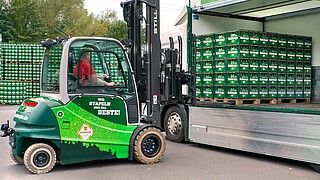
Nazwa: Westerwald-Brauerei
Obszar działalności: produkcja piwa – ze szczególnym uwzględnieniem piw typu pilzneńskiego
Miejsce wdrożenia: Hachenburg, Niemcy
Westerwald to jeden z najstarszych browarów warzących w Niemczech piwa typu pilzner. Stworzone w 1861 r. przez Heinricha Schneidera przedsiębiorstwo pozostaje niezależną firmą, którą zarządza obecnie piąte pokolenie rodziny założyciela. Asortyment produktów obejmuje dziś piwa 10 rodzajów sprzedawane pod markami Hachenburger oraz Westerwald-Bräu. Motto firmy brzmi „Zachowywać to, co dobre i być otwartym na nowe”. Jego odzwierciedleniem jest warzenie piwa w zgodzie z tradycyjnymi metodami i maksymalna dbałość o utrzymanie wysokiej jakości produktu przy jednoczesnym poszukiwaniu innowacji i niekonwencjonalnych dróg dążenia do tego celu. Przykładem realizacji tych założeń jest niedawna modernizacja należącej do browaru floty transportu wewnętrznego.
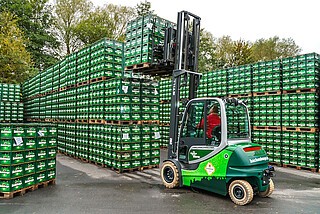
Cel wdrożenia oraz zastosowane rozwiązania intralogistyczne
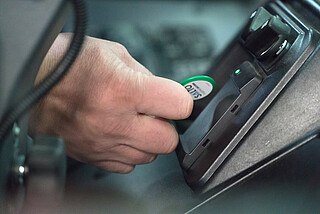
Cel wdrożenia:
- Zwiększenie ergonomii pracy operatorów wózków widłowych
- Zmniejszenie śladu węglowego floty intralogistycznej
Wdrożone rozwiązanie:
- Całkowite zastąpienie spalinowych wózków widłowych pojazdami elektrycznymi, w tym m.in. czołowymi wózkami widłowymi z przeciwwagą napędzanych silnikami elektrycznymi serii RX 60-25 i RX 60-50
Mając na uwadze kwestie ochrony środowiska i ergonomię pracy operatorów, w Browarze Westerwald wdrożono nowoczesne, wysokowydajne wózki elektryczne o udźwigu do 5 t. Do sztaplowania wyrobów gotowych zastosowano wózki elektryczne STILL RX 60-50 z podwójnymi widłami. Dzięki udźwigowi maksymalnemu na poziomie 5 ton są one w stanie skutecznie podnosić dwie wypełnione kratami piwa palety na znaczne wysokości. Uzupełnieniem floty są mniejsze, bardziej kompaktowe wózki RX 60-25. Wszystkie nowe maszyny zintegrowano z systemem zarządzania flotą STILL FleetManager oraz wyposażono w szereg udogodnień z obszaru energooszczędności oraz ergonomii i bezpieczeństwa pracy. By usprawnić odkładanie i pobieranie palet, w części wózków wykorzystano hydraulicznie wyciągane w przód widły. By zapewnić komfortową pracę wewnątrz i na zewnątrz magazynu – niezależnie od pory roku i dnia – kabiny pojazdów są ogrzewane. By natomiast zwiększyć bezpieczeństwo w ruchu dzięki poprawie widoczności wózków, wyposażono je w komplet reflektorów w pakiecie STILL Safety Light.
Efekty wdrożenia i wynikające z niego korzyści
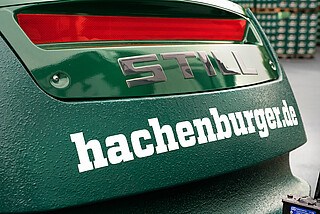
Zwiększenie komfortu pracy operatorów
- Poprawa bezpieczeństwa pracy wózków
- Zmniejszenie kosztów eksploatacji
- Całkowite przejście browaru na odnawialne źródła energii
Przejście na bezemisyjne czołowe wózki elektryczne dało większą swobodę w ich wykorzystaniu– bez ograniczeń związanych z użytkowaniem pojazdów na LPG w zamkniętych pomieszczeniach. Dzięki braku wibracji, zastosowaniu siedzisk z pneumatyczną amortyzacją i mniejszemu natężeniu hałasu poprawił się także komfort pracy operatorów. Kontrolujący dostęp do wózków oraz rejestrujący kolizje system STILL FleetManager zwiększył ostrożność pracowników podczas wykonywania zadań. Rozwiązanie znacząco przełożyło się także na obniżenie kosztów eksploatacji. Standardowo stosowany w elektrycznych wózkach STILL program oszczędnego gospodarowania energią pojazdu, Blue-Q, zmniejszył jej pobory nawet o 20 proc. Co więcej, dzięki wykorzystaniu źródeł odnawialnych, cały browar – w tym procesy transportu wewnętrznego – są w całości zasilanie „zieloną” energią.
– Zrównoważony rozwój i przyjazność środowisku to dla naszej firmy istotne kwestie. W 2017 roku uzyskaliśmy ogromne oszczędności dzięki modernizacji parku maszynowego oraz systemu chłodzenia. Teraz w ten trend wpisują się także nasze nowe wózki widłowe – konkluduje Jens Geimer.
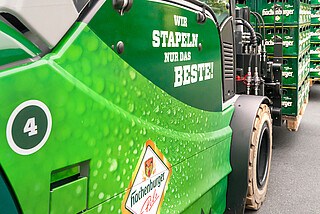